SMART PACKAGING & PRINTED ELECTRONICS
Testing requirements for smart packaging: Ensuring quality, safety and functionality
Doro Mergner of MSWtech, Nuremberg, Germany, takes a look at the essential testing requirements that are critical when using flexible electr onics in packaging.
In today’s globalised world, packaging plays a central role in transporting and protecting products. The requirements for packaging materials are crucial to ensure that these materials maintain the quality, safety and functionality of the products they contain. Given the wide variety of products and the diverse requirements in different industries, packaging testing is complex and multifaceted.
Mechanical tests Tensile, compression and impact resistance
Tensile, compression and impact resistance tests are essential to measure the ability of packaging materials to withstand various forces. These tests are crucial to ensure that packaging will not tear or break during transport and handling.
They can be carried out at the MSWtech test centre in Nuremberg, Germany, where the required force is measured to ensure that the materials meet the requirements.
Twisting, folding, rolling, sliding
These types of test variables are particularly important for functional components in packaging, such as RFID, NFC, LEDs, e-paper, temperature sensors, humidity sensors, batteries, QR codes, and many other possibilities offered by flexible electronics. As the tests are carried out with regular electrical measurements, the point at which degradation begins is immediately identified and documented. This option is based on the Flexdata software from the American collaboration partner BayflexSolutions.
Environmental durability testing
Global markets require a variety of transport methods that expose to a wide range of stresses. Consumers expect assurances about the durability, functionality and quality of their goods. These assurances can only be validated through robust testing. The MSWtech test centre also offers climatic tests to accelerate mechanical stress, such as temperature and humidity tests, which examine the reaction of packaging materials to different temperature and humidity conditions. Packaging that is transported or stored in different climatic zones must remain stable under extreme conditions. At the same time, these results can be incorporated into ageing and weathering tests.

Packaging testing, especially with the integration of flexible electronics, is essential to ensure the quality, safety and functionality of the products they contain.
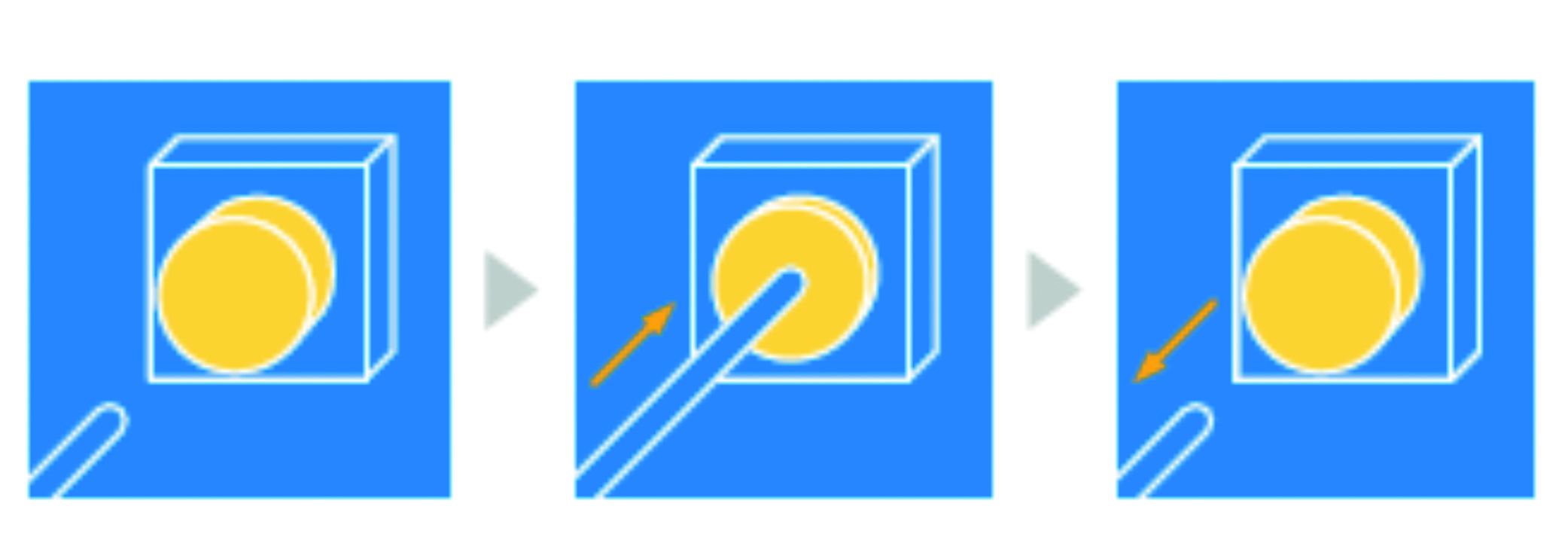
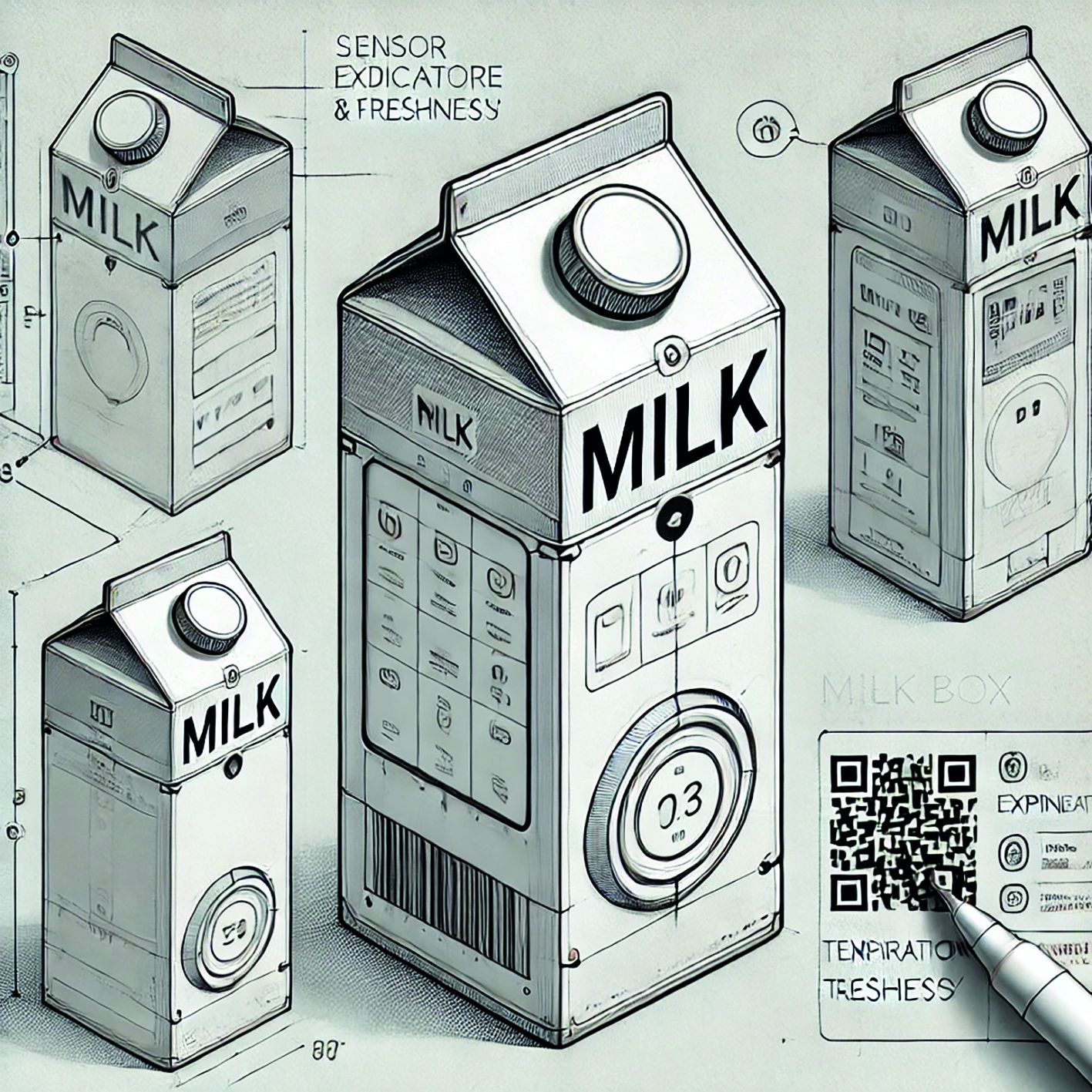
An AI-generated vision of a smart milk box with several functions.
Regulatory and standards compliance ISO and ASTM standards
Packaging materials often need to comply with international standards set by organisations such as ISO (International Organisation for Standardisation) and ASTM (American Society for and Materials).
Industry-specific regulations
Different industries have specific regulations and standards that must be to comply with legal and safety requirements. Flexible electronics are new products and their development is progressing rapidly. Existing standards and norms are often no longer applicable or sufficient. Various international commissions are actively working on this topic. Testing is also essential in this area.
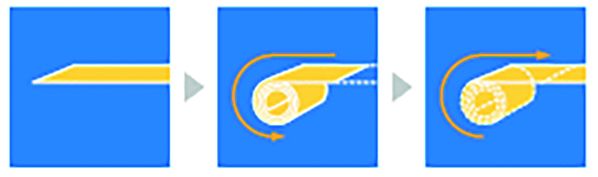
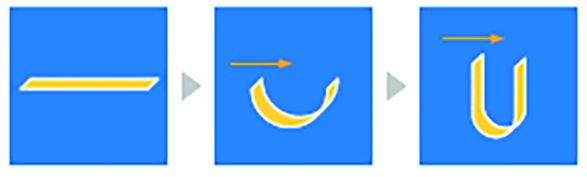
To measure the ability of packaging materials to withstand different forces, tensile, compression and impact tests are essential.
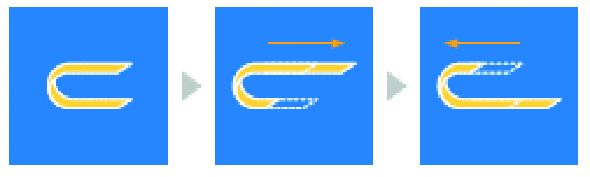
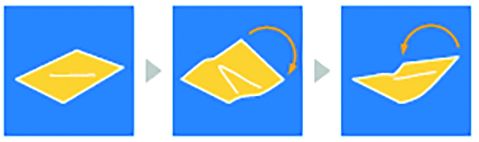
Conclusion
In an increasingly globalised and technology-driven world, the demands on packaging materials and technologies are higher than ever before. Packaging testing, especially with the integration of flexible electronics, is essential to ensure the quality, safety, and functionality of the products they contain. Mechanical stress testing, environmental durability testing and regulatory compliance are critical. They ensure not only the physical integrity of the packaging, but also the reliability of the electronic components it contains. Advances in flexible electronics, such as RFID, NFC, LEDs and sensors, require new test methods and adjustments to existing standards and norms. Without careful and comprehensive testing, innovations in packaging technology could not fully realise their potential benefits. Ultimately, testing of packaging materials and systems is not only technical necessity, but also a key component of product development and safety. It ensures that packaging is fit for purpose and can meet the challenges of modern supply chains, while meeting consumer expectations and international standards. In a world where packaging is increasingly taking on intelligent functions, robust test methods are key to the success and market acceptance of these new technologies.
www.mswtech.de www.bayflextechnologies.com
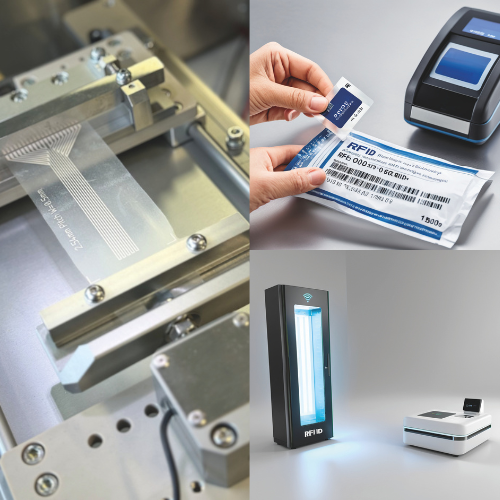
Advances in flexible electronics, such as RFID, NFC, LEDs and sensors, require new test methods and adjustments to existing standards and norms.
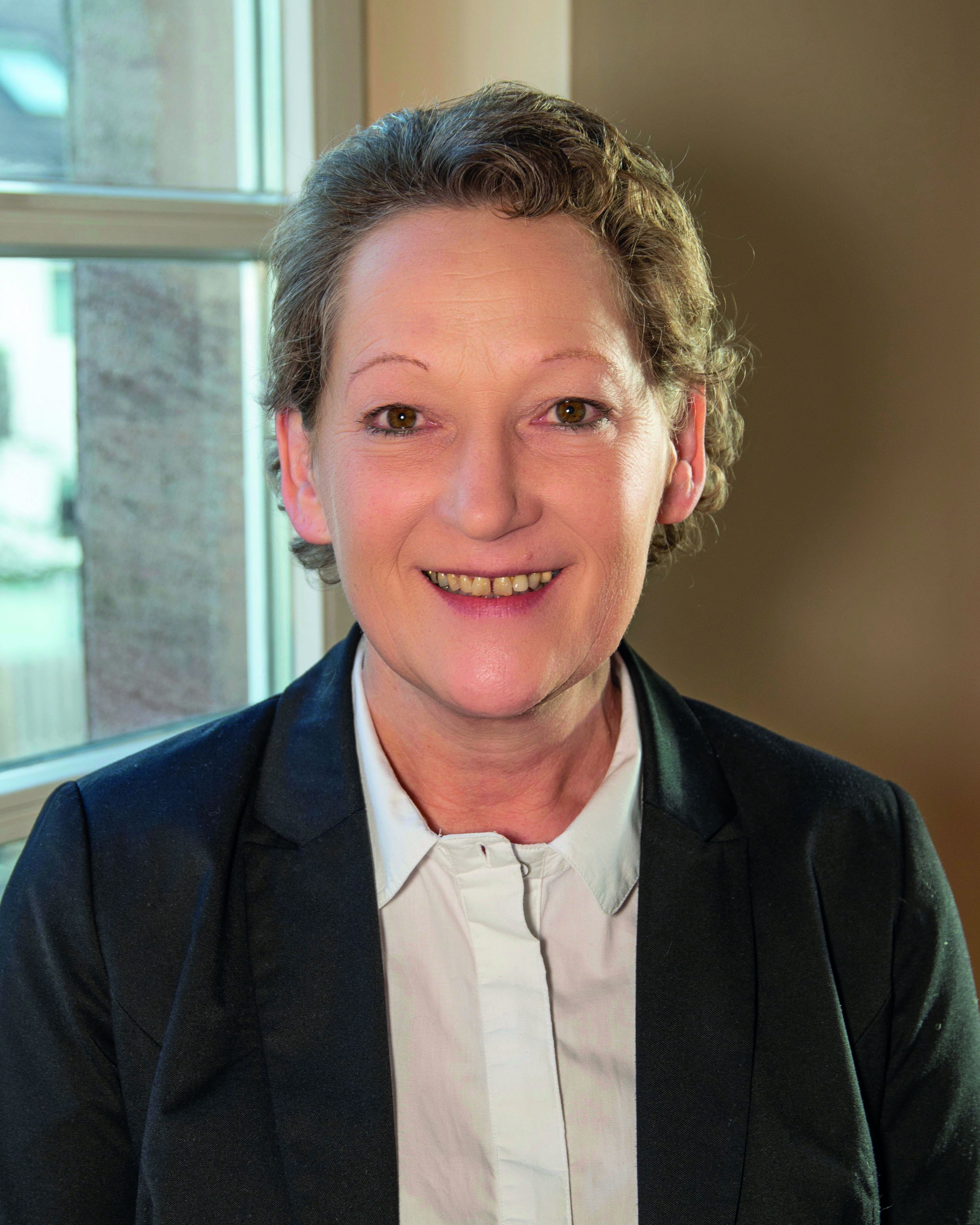
THE AUTHOR Doro Mergner, a qualified chemical technical assistant, embarked on a career change over two decades ago to delve into printed and flexible electronics. Her professional journey started at Siemens AG, where she contributed to the development of OLEDs. Subsequently, she transitioned to PolyIC GmbH & Co. KG, focusing on the development of integrated circuits and transparent conductive films. Currently serving as a project manager, Doro Mergner collaborates with Wolfgang Mildner of MSWtech to establish the Nuremberg test centre for flexible electronics. Her task at hand involves defining and implementing tests as part of the journey towards standardisation.
MSWtech Founded by Wolfgang Mildner and initially rooted in software development, MSWtech has established a testing facility in Nuremberg, Germany, in collaboration with BayflexSolutions from the USA. The company specialises in the analysis of technologies, particularly in the field of printed electronics. It brings together technical and market expertise and uses mechanical testing equipment from Japanese manufacturer Yuasa Systems. Services encompass the examination of mechanical stress factors such as stretching, flexing and bending as well as data acquisition, storage and trend analysis. The testing facility enables stress tests without customers needing to provide own resources or own equipment.