WEARABLES
Advancing wearable technology: Digital inkjet printed flexible strain sensors on textiles
Advances in digital inkjet printing demonstrate the possibility of functionalising textiles in an unprecedented way. A new solution, developed by Profactor, Steyr, Austria, in cooperation with ITP, Weimar, Germany, for seamlessly integrating a strain-sensing sensor onto a textile-based tape shows versatility across multiple industries and has the potential to revolutionise certain sectors.

Figure 1: Sketch of the strain-sensing sensor realised on textiles. Corresponding material layer stack of the strain-sensing device (from left). Image: Profactor
In cooperation with ITP, Profactor has developed a solution to utilise additive manufacturing techniques to integrate a strain-sensing sensor seamlessly onto the textile-based CondElastX tape by combining direct-to-garment printing of a multimaterial electronic island with dispensing of a piezoresistive strain gauge (see Figure 1). The fully inkjet-printed electronic island consists of a conductive silver nanoparticle layer forming the electric circuit, which is encapsulated between a rigid dielectric planarisation layer and a passivation layer. The current and signal transmission of the strain sensor system occurs via the four integrated conductive strands of the CondElastX tape. This solution offers the potential for a wide range of strain-sensing applications on flexible and stretchable substrates, allowing for a high degree of customisation regarding the size of the electronic island, the position and the number of integrated strain gauges. The innovative integration of a digital inkjet-printed strain sensor onto the stretchable and conductive CondElastX tape from ITP textiles marks a pioneering advancement in smart textiles. Due to their high efficiency and on-demand production capability, industrial inkjet printers typically consume less energy in comparison to standard screen printing technologies, resulting in lower emissions. Furthermore, inkjet printing has a lower material consumption because of the drop-on-demand operation combined with its high
accuracy, which reduces waste materials and the environmental impact. This development aims to enhance the capabilities of wearable technologies, facilitating the transition towards a modern digital society through advanced data collection. Smart textiles can significantly enhance safety-related aspects, such as work safety in hazardous environments by monitoring physiological parameters and facilitating communication. Simultaneously, they reduce device weight, increasing operational freedom. Additional applications include sports activity monitoring, fitness sensor bands and personalised patient monitoring devices for tracking respiratory rates and other vital signs. ITP’s existing product CondElastX is an elastic tape with four conductive and stretch-independent strands. The different variants in design and appearance are ideal for and signal transmission of electronic components in the smart textile sector. CondElastX is manufactured through a web process, which results in a limitation of customisation for certain applications, e.g. sensors. The digital integration of a sensor system on the CondElastX requires contacting the insulated conducting lines on the CondElastX tape. This was successfully achieved by punctuated laser abrasion, whereby only the insulation of the copper wires was melted at specific points (see Figure 2a) without damaging the textile underneath

Picture A

Picture D

Picture B
Figure 2: a) Melted cupper wire after laser abrasion; b) Direct-to- garment inkjet-printed electronic island for readout electronic; c) Threefold characterisation of the resistance response in dependence of progressively increasing cyclic load; d) Dispensing carbon-based strain gauge on TPU interposer. Images: Profactor
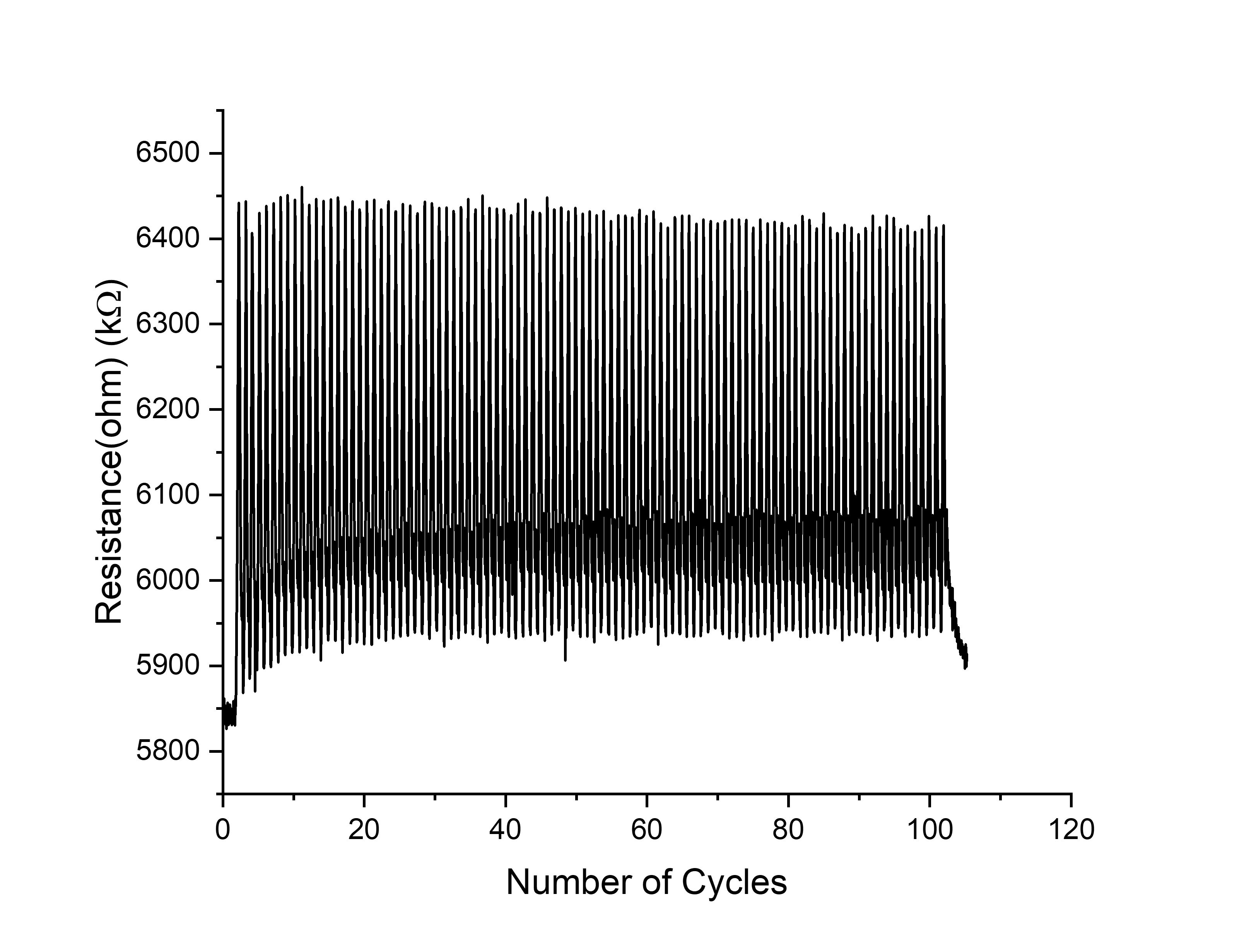
Picture C
In order to establish a more stable and reliable electrical connection, the contact point was dispensed with a drop of conductive silver adhesive. The corresponding electronics (readout circuit, loT) are printed on designated dielectric island structures using digital inkjet printing (see Figure 2b). The dielectric encapsulation serves, on the one hand, as a rigid planarisation layer to ensure a flat surface for printing the electric circuit on top, and on the other hand, as passivation against mechanical impact and moisture to ensure electrical integrity. The strain-sensing layer (see figure 2d) was printed onto the CondElastX by dispensing conductive and stretchable carbon ink and stretchable TPU passivation to enhance the mechanical and electrical reliability of the system. Characterisation of the sensitivity of the strain sensor was analysed with a cyclic tensile test (see Figure 2d). The trifold determination of the resistance curves as a function of progressively increasing cycles with an applied strain of 0.08 and a corresponding elongation of 2 mm within a period of 6s. The strain-sensing system could endure a maximum elongation of 350%, corresponding to an external load of 120N without disrupting the conductive lines nor the dispensed strain gauge. After exposure of approximately 100N, the electrical signal was lost. As soon as the system is relieved from the load, the electrical signal is reestablished. ITP has designed a circuit tailored to evaluate the printed strain gauge, fitting within the dimensions of the CondElastX tape. Communication between the circuit and the strain gauge occurs via the four conductive strands on the CondElastX, utilising the RS485 bus. To minimise energy consumption, the measuring system only performs digitisation of the measured values, without any additional processing. This development demonstrates a novel approach to manufacturing a seamlessly integrated, robust wearable strainsensing device directly onto the CondElastX tape by combining multiple digital deposition technologies. While the proof of concept was demonstrated in a laboratory setting, this approach can be scaled up for industrial production. The newly developed strain-sensing sensor shows versatility across multiple industries. lt offers potential applications outdoor products such as backpacks, tents and tarps, enabling precise monitoring of weight distribution for enhanced durability and lifetime assessment. In the medical field, integrating these sensors into textiles enables continuous patient monitoring, providing real-time health data for improved care. Moreover, the sensors could revolutionise aerospace and automotive industries by monitoring seat cushions for real-time data on occupancy and comfort, ensuring optimal conditions over extended periods.
www.profactor.at www.itp-gmbh.de
ABOUT PROFACTOR Profactor GmbH, founded in 1995 and headquartered in Steyr, Austria, is a research company focusing on functional surfaces and nanostructures, robotics and machine vision. Approximately 100 scientists from various disciplines conduct research to improve the competitiveness of the production industry and strengthen both Austrian and European industry. Profactor covers the entire range from basic research to applied research, closing the innovation gap between research results and market introduction.
ABOUT ITP ITP GmbH, Weimar, Germany, has been a service provider and R&D partner for new intelligent textile products for over 20 years. The company develops components for intelligent textiles, such as sensors, conductive textile components, electronic modules and prototypes. ITP also develops technologies for integrating sensors into different materials, tests prototypes in house and creates manufacturing processes for series production. Prototypes of intelligent textiles are being developed for the medical, sports, personal protective equipment and automotive sectors.