PRINTING TECHNOLOGY
The role of automation in small-batch screen printing for printed electronics
Automation in small-batch screen printing is transforming the production of printed electronics by significantly reducing set-up times and increasing efficiency, which is essential to meet the growing demand for customised products. These technological advances not only improve productivity and print quality, but also support more sustainable manufacturing practices, says Katja Pirnat of Slovenian screen printing machinery manufacturer INO.
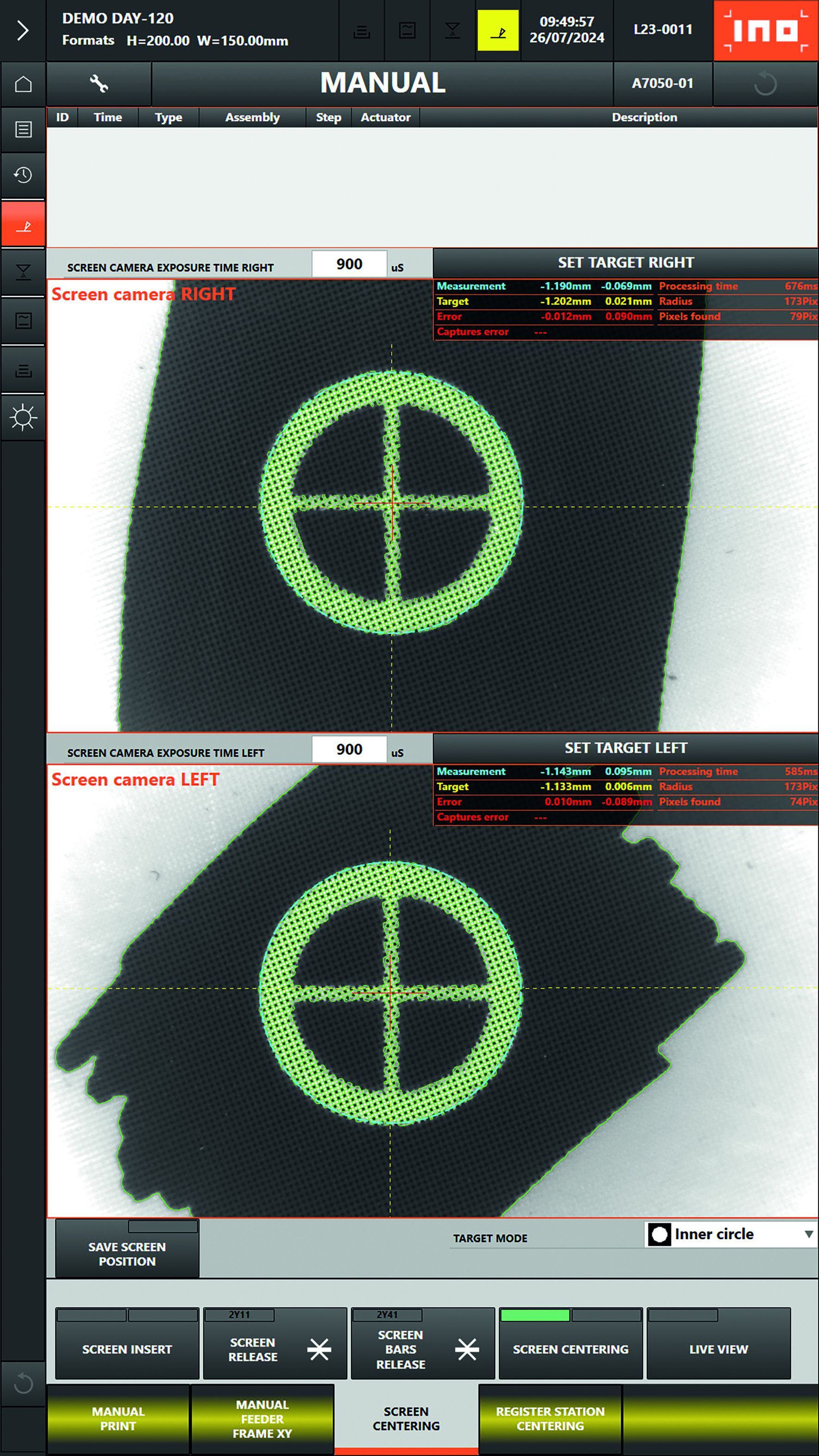
At the push of a button, the screens are automatically positioned using three servo motors. The fully automatic screen positioning function reduces screen change time by a factor of 5. Images: INO
Decades of work and research have led to a point where the proportion of devices containing printed electronic elements is increasing daily. The need for rapid prototype-to-production transfer and market demand for customised products dictate small production runs and cost-effective equipment. Flatbed screen printing, when enhanced by automation and optimisation of key processes, is one of the techniques that enables high quality and competitive small-batch production.
Challenges of screen printing
The screen printing method is suitable for producing printed components for various applications. Its ability to use a wide range of printing pastes and substrates makes it well-represented in the printed electronics industry. However, it faces several significant challenges. When not highly automated, screen printing is a relatively slow process. High set-up times with each screen change lead to long idle phases and the extension of the time required to complete a batch. This reduces production efficiency and increases costs. The issue is particularly pronounced in short runs, where frequent setups within a brief period exacerbate the problem. It quickly becomes apparent that low-volume production incurs substantial costs from a manufacturing perspective.
Automation of key processes
The introduction of new technological innovations and automated processes into this traditional and relatively simple technique has a significant impact on the development and competitiveness of screen printing. One key innovation is the automatic screen positioning system, which uses servo motors and stores repeatable positions to allow quick and precise screen setup. The operator initiates the process with the press of a button, minimising the influence of human error on quality and time consumption. This fully automatic function reduces set-up or screen change time by a factor of 5 compared to conventional procedures. The automated process also significantly decreases the amount of wasted material generated during setup. Additionally, reduced energy consumption and waste contribute to lower costs and more sustainable production.
Case study: Changeover speed is crucial
The analysis was conducted on the membrane keyboard printing process, which is still the most widely used product involving a printed circuit. In addition to printing the conductive layer, we also printed the graphic layer, both requiring a total of four passes. We tracked the print time for one batch in 20 production cases using fully automatic screen positioning on the INO A7 line and compared it with the time required for the setup on other equipment. While printing press speed might seem like a decisive factor for achieving a shorter printing time, a closer examination reveals a more complex picture. Even with just four screen changes, the impact of changeover speed on the total print time becomes apparent. As the number of prints and the batch size increase, the time savingsbecome even more pronounced. The automatic setup completes this crucial phase in less than two minutes, compared to an average of ten minutes or more for other setup methods. Reducing setup time improves overall utilisation throughout the print process, minimising idle time and maximising production output. Although other screen printing equipment offers higher speeds for large batches, for printed electronics projects, where smaller batches are typical, screen change speed is critical.
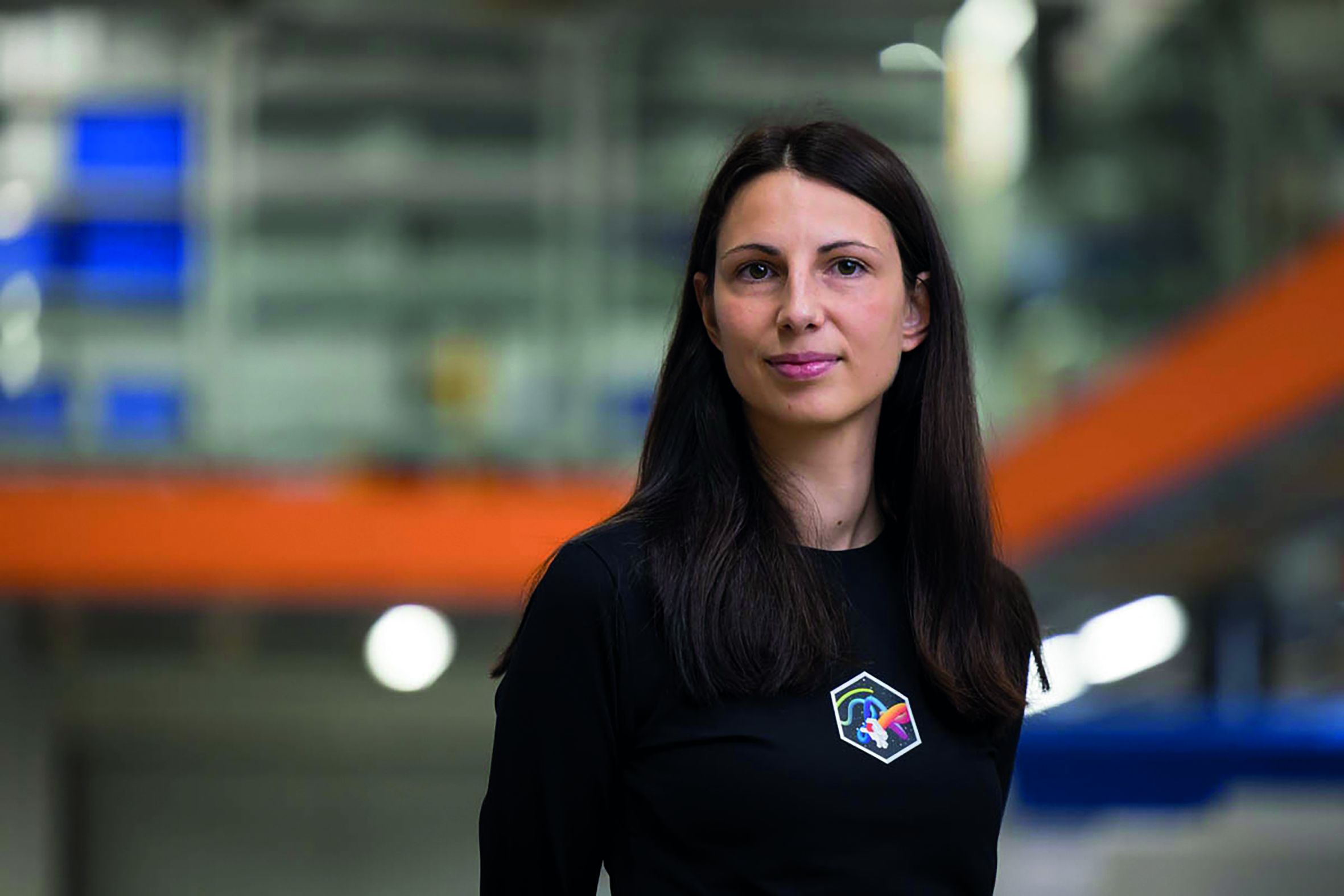
THE AUTHOR Katja Pirnat is a screen printing expert at INO. She is experienced in printing technology and materials with relevant customer and market insights.
THE COMPANY INO, based in Žiri, Slovenia, specialises in the development and manufacture of screen printing machines. With over 30 years of experience in screen printing and automation, INO’s team of 20 developers and researchers is creating significant advances in screen printing technology. The company operates globally, providing solutions that increase production efficiency in printed electronics and screen printing in general. www.ino-ziri.si
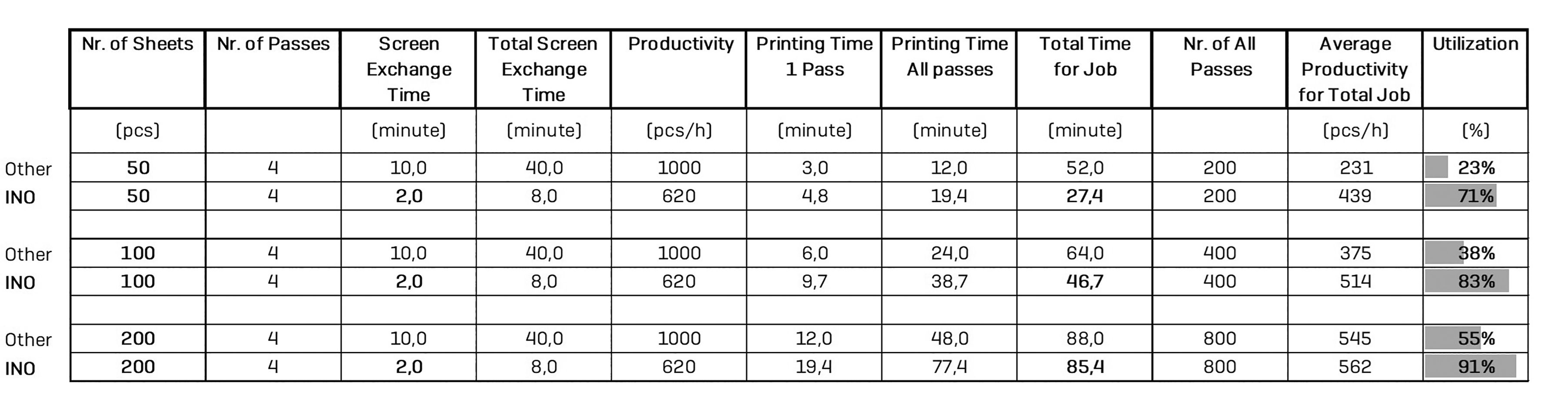
The table shows the printing time of the entire batch with quantities of 50, 100 and 200 pieces for four print passes, comparing fully automatic screen positioning (ASP) with other setup methods.
Significant benefits to the industry Highly automated screen printing technology offers significant benefits to the printed electronics industry, particularly in small-batch printing. Automating screen setup significantly reduces production time, increases productivity and
improves print quality. In addition, lower energy consumption and waste reduction contribute to lower costs and a more sustainable production. These solutions are essential to meet the demands of modern manufacturing and maintain a competitive edge in the printed electronics industry.
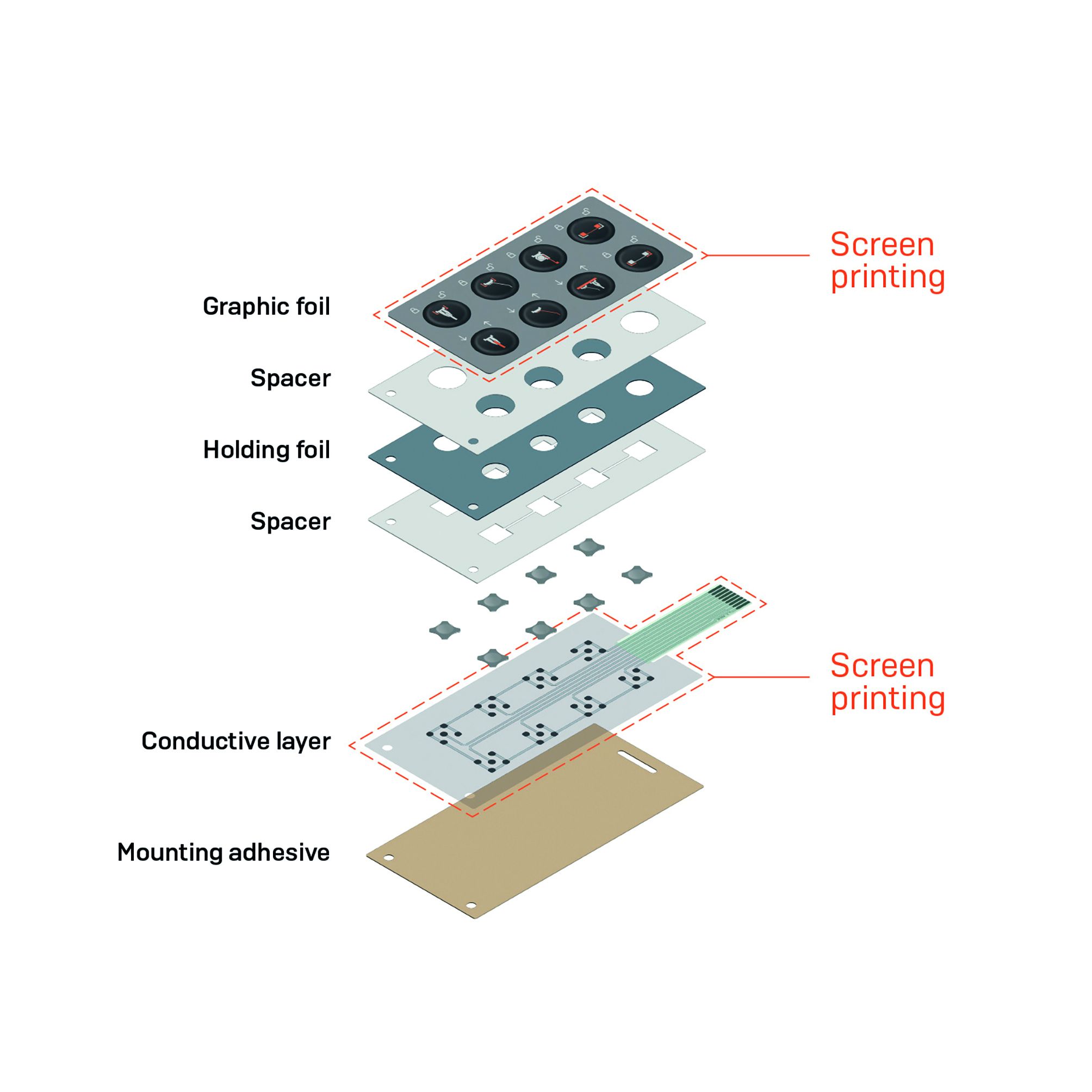
Construction of a membrane keyboard, the most widely used industrial product involving a screen printed circuit.
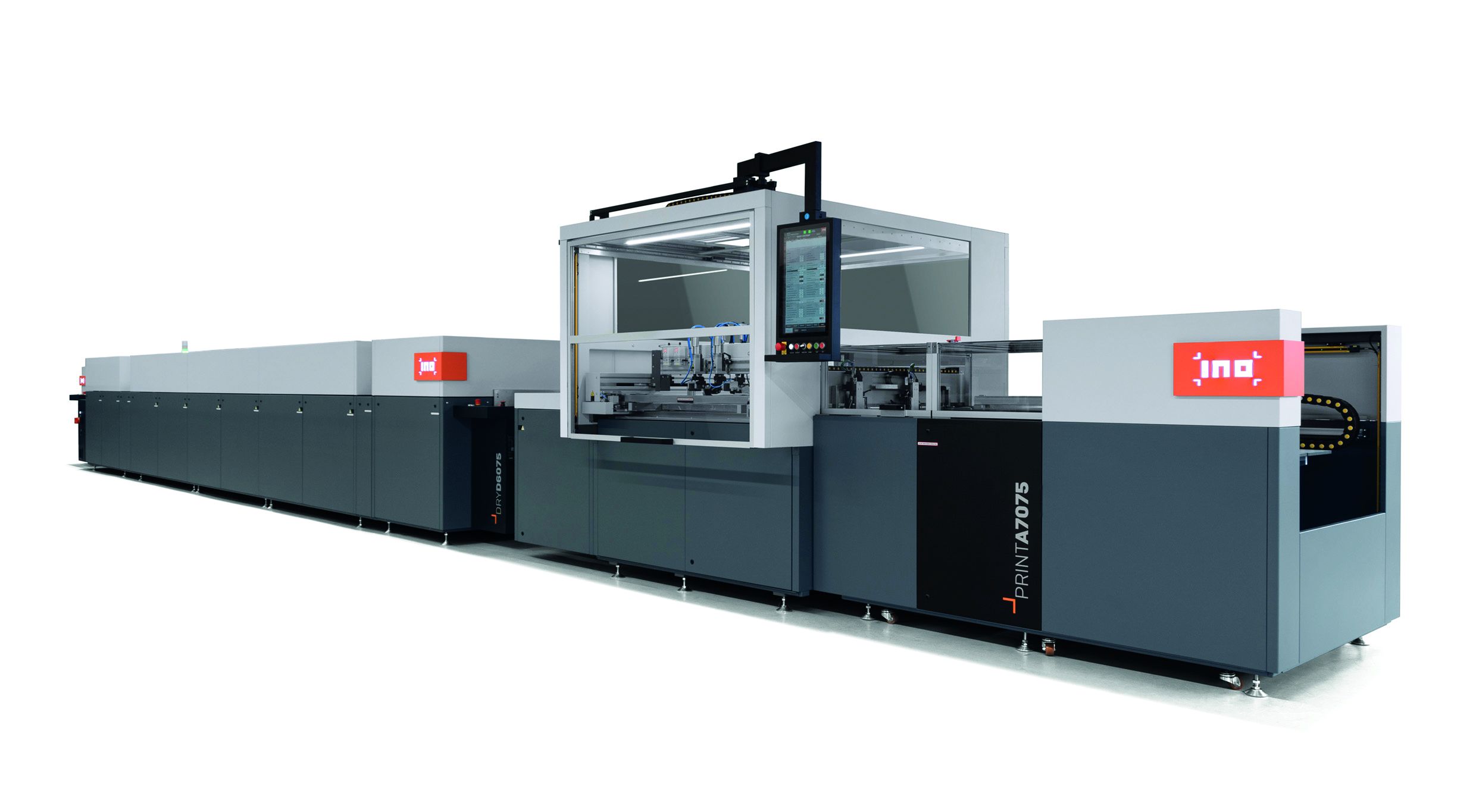
INO A7 line: The highly automated screen printing technology offers significant advantages for the printed electronics industry, particularly in small-batch printing.