WEARABLES
New perspectives in reliability testing and performance qualification for wearables
For many wearable devices, including medical devices, “never fail” is a critical attribute that needs to be optimised for device performance, so there is an emerging need for continuous performance monitoring and testing, writes Eisuke Tsuyuzaki, founder and Managing Director of Bayflex Solutions in San Jose, California
Visiting the annual Consumer Electronics Show in Las Vegas, we saw an explosion of hardware products, now harnessing the computing power made possible with cloud and artificial intelligence tools. Perhaps wearables cover the widest area of printed electronics technology, from the largest product segment of printed displays such as OLED devices, to a wide range of thin, flexible, wired and wireless sensors and communication protocols for monitoring vital signs, to e-textiles using on-yarn stretchable components or in-yarn fabrics with infinite power. As a reflection of our printed and organic electronics community, wearables represent one of the most diverse sets of products and systems, and therefore different reliability test methods and product performance qualifications.
Reflecting user experience
Recently at SID in San Jose, the display industry’s flagship event, it became clear that while basic OLED assessment methods using a clamshell flexing tester remain steadfast, subtle product configurations with hinge mechanisms require some real and realistic assessments that reflect complex user experiences (mimicking how a user might open and hold a screen before closing, not just simple mechanical repetition over a quarter of a million cycles). This year we saw more device offerings for wearables beyond consumer devices, but in harsh outdoor conditions. To date, the state of the art has been passive testing in single-use environmental chambers (temperature and humidity, vibration or rain chambers) defined by the automotive or military systems industries. The US MIL 810H specifications provide detailed microelectronics methodologies that include mechanical shock, liquid/gas immersion, dust/dirt or altitude and must now be considered for both passive and integrating multi-axis motion.
Advanced simulation
Aside from mechanical testing and the integration of extreme hostile conditions, we can see improvements just over the horizon to incorporate 3D components that will enable computeraided software to design virtual models of devices and simulate stress testing, thermal analysis and even fluid dynamics. While digital prototyping can reduce assessments costs, hardware prototypes also need to be reproduced in the real world, making it more important to have accurate, repeatable, commercial-grade test systems. Such advanced simulation and modelling could also be used to ensure that electronic sensors work properly, including audio, vital signs and bio-fluid status monitoring.
Machine learning
In order to process a huge of data, we can turn to machine learning techniques. First, after running numerous experiments, we can determine the performance degradation of a single electronic data point, such as resistance. In the next test, following a best-fit curve, it will be easier not only to predict, but also to selfcorrect, if necessary, to change the state to preserve the useful life of the product. With multiple individual data points, we are able to build more sophisticated data framework models from multiple sensors (e.g. resistance, temperature, humidity) to more accurately predict failure modes. Finally, we are beginning to see the integration of various imaging systems (optical, infrared, X-ray, CT) to capture the evolution of metal fatigue. Over numerous samples, with the use of generic AI computer vision tools (e.g. segmentation, rotation, light, measurement) or filters, the system can be trained to automatically detect anomalies to develop a more sophisticated product reliability tool for supplier qualification or more valuable licensing opportunities. Eisuke Tsuyuzaki
ABOUT BAYFLEX SOLUTIONS Bayflex Solutions, headquartered in San Jose (California, USA), a developer of lab automation and data (with mechanical and climate integration), continues to serve the printed and organic electronics industries, including wearables of printed displays, electronic components and e-textile substrates. It is currently developing its AI tools Flexdata.Bobbi (AI prompt and perform test methods) and Flexdata.Leonardo (ML and AI anomaly detection) based on the real needs of global and high-impact organisations. In addition, the company has recently opened a testing centre specifically for European clients to provide consulting and assessments from Germany, infused with global best practices.
www.bayflextechnologies.com
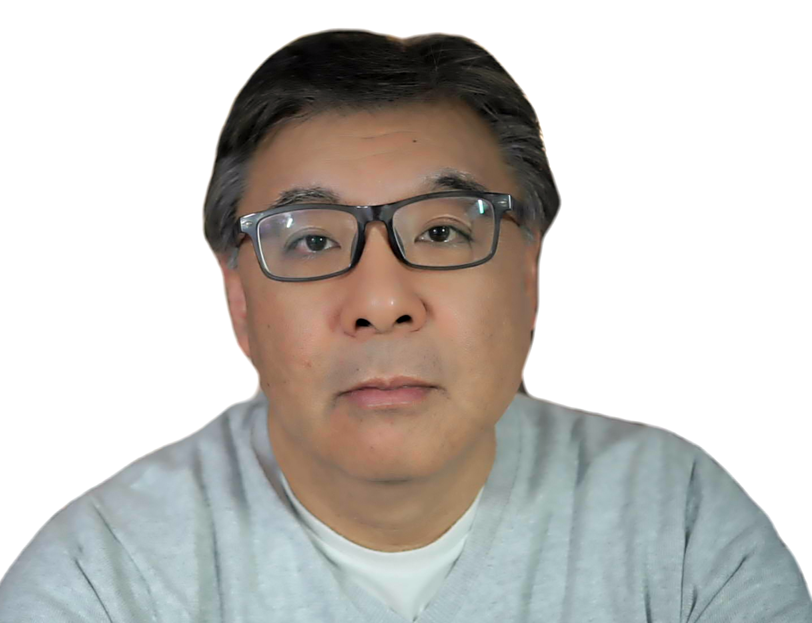
THE AUTHOR
Eisuke Tsuyuzaki is the founder, owner and Managing Director of Bayflex Solutions, which develops lab automation and analytics tools for reliability test systems used in flexible electronics research, product design and manufacturing in North America, Europe and Middle East. He currently serves as an advisor to the Executive Committee of SEMI/FLEXtech. In addition, Tsuyuzaki is an early-stage investor in flexible electronics adventures. He was a mentor at Nex3 and a leader in early-stage innovation and start-up acceleration in Silicon Valley. Previously he has won an Emmy and was Chief Technology Officer at Panasonic. He has also worked in corporate planning at Sony Corporation in Tokyo and at Sony Pictures Entertainment in Los Angeles. Educated in Europe, Tsuyuzaki now lives in San Jose, California. He is a graduate of SophiaUniversity in Tokyo, Japan, the University of California, Los Angeles, and Stanford University.