RESEARCH & DEVELOPMENT
“A milestone in battery research”
A unique competence centre for the research and production of battery cells is being built in Münster, Germany. The new facility will make a significant contribution to advancing the production of battery cells made in Germany and strengthening the country as a centre of technology.
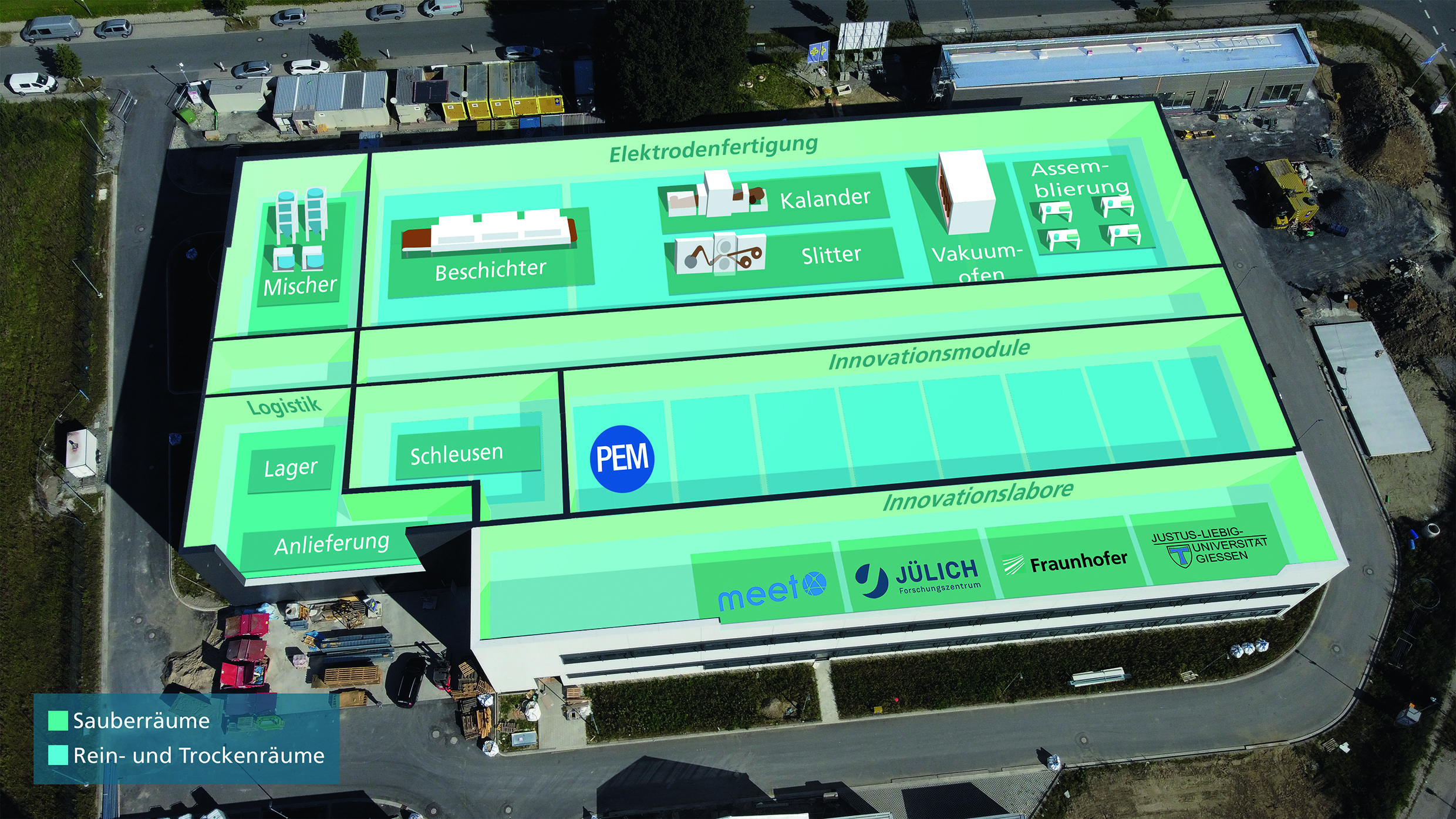
With the launch of the facility, Fraunhofer FFB begins research activities at the site, utilising cutting-edge European machinery technology. Image source: Fraunhofer FFB
Battery and storage technologies are crucial for the success of the energy and transport transition. According to a study by the Fraunhofer Institute for Systems and Innovation Research (Fraunhofer ISI), battery production capacity in Europe alone will quadruple by 2025 from 124 gigawatt hours in 2022 to over 500 gigawatt hours. By 2030, this figure is expected to increase tenfold to up to 1.5 terawatt hours. Given these projections, the largest German and Europewide unique competence center for developing and testing the production of battery cells – including for electrically powered vehicles – is currently being built in the Westphalian city of Münster: the Fraunhofer Research Institution for Battery Cell Production FFB (“Fraunhofer FFB”) The first phase, the “FFB PreFab”, was inaugurated with around 500 guests at the Hansa-BusinessPark in Münster at the end of April, an important step on the way to building the FFB Fab. Upon completion, the FFB Fab will offer an extra 20,000 m² dedicated to production and research, facilitating large-scale industrial research and development in the gigawatt range using plant technology in Münster. The opening marked “a significant milestone for the Fraunhofer-Gesellschaft, the FFB battery cell research production, and most importantly, for sustainable and competitive battery production in Europe,” said Prof Holger Hanselka, President of the Fraunhofer- Gesellschaft, on the occasion of the inauguration.
Full-scale battery cell production With its two facilities, PreFab and Fab, Fraunhofer FFB is currently one of the largest construction projects for research in Germany and also unique globally. Research operations are now starting in the FFB PreFab with the commissioning of innovative European machine technology on 6800 m² of research space. A demonstration line for full-scale battery cell production allows the Fraunhofer FFB to assist its industrial partners in the trial and adoption of novel battery cell designs and production methods. The facility specialises in producing pouch and prismatic cells for research applications, which are utilised in electric vehicles, medical technology and smart devices. The Federal Ministry of Education and Research (BMBF) and the state of North Rhine-Westphalia are funding the establishment of the facility as part of the “FoFeBat” project with up to €820 million altogether. The Fraunhofer Gesellschaft is gradually realising the project with several partners. These include, for example, Siemens AG, which is supporting the Fraunhofer FFB with software and hardware solutions based on the open Siemens Xcelerator platform. With their interoperable systems, the Digital Industries and Smart Infrastructure business units are contributing to the digitisation, automation, control and monitoring of the machines, processes and building.
A digital twin reflects the factory
The real production and environmental conditions in the facility are being digitally mapped along the entire value chain by connecting operational technology to information technology. Sensors in the building and throughout the production environment will provide all relevant infrastructure data in real time. Using the manufacturing execution system (MES) and the IIoT platform (industrial internet of things), Fraunhofer FFB will be able to plan, control, optimise and flexibly scale its processes, explains Siemens. The Desigo CC building management platform will determine the optimal production environment with data-based and demand-oriented processes, even in clean-rooms and drying operations. The collected data will be of central importance for Fraunhofer FFB in fulfilling its mission of researching the production of battery cells using a digital twin of the factory. The digital twin reflects the entire factory, from the technical building equipment to all production processes. This guarantees production under near-series and difficult conditions, e.g., clean room production, for a variety of industrial partners.
Following the inauguration of the FFB PreFab recently, test areas, so-called innovation modules, are now available for partners from various industries and other research institutions. These test areas enable the temporary accommodation of systems for testing and further development together with project partners. As Fraunhofer FFB explains, technology maturity progresses from the laboratory to the innovation module, and finally to the production line, all housed under one roof. “Innovation and commercialisation processes are thus driven forward. The risks when transferring novel cell concepts and production technologies to large-scale production are reduced.” Around 125 people are currently employed at the Fraunhofer FFB. The region is also set to benefit from the project’s appeal: Together with the MEET (Münster electrochemical energy technology) facility at the University of Münster and other research partners from Aachen, Jülich and across Germany, the “battery city” Münster could become a key economic and technology centre in Germany and Europe.
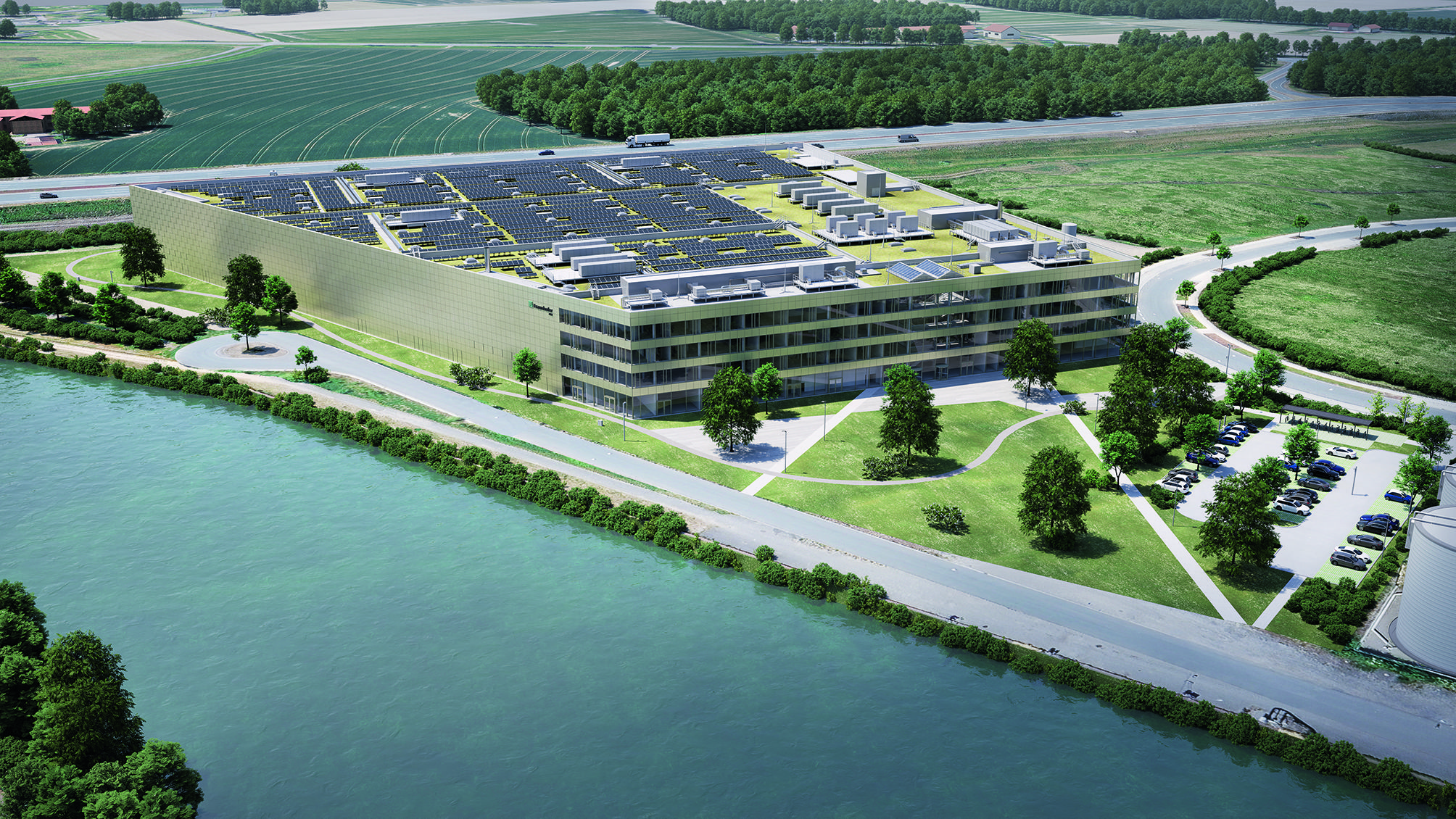
The Fraunhofer FFB in Münster, Germany, is supposed to play a pivotal role in enhancing the production of Germanmade battery cells. Image source: Fraunhofer FFB/ARTVISU
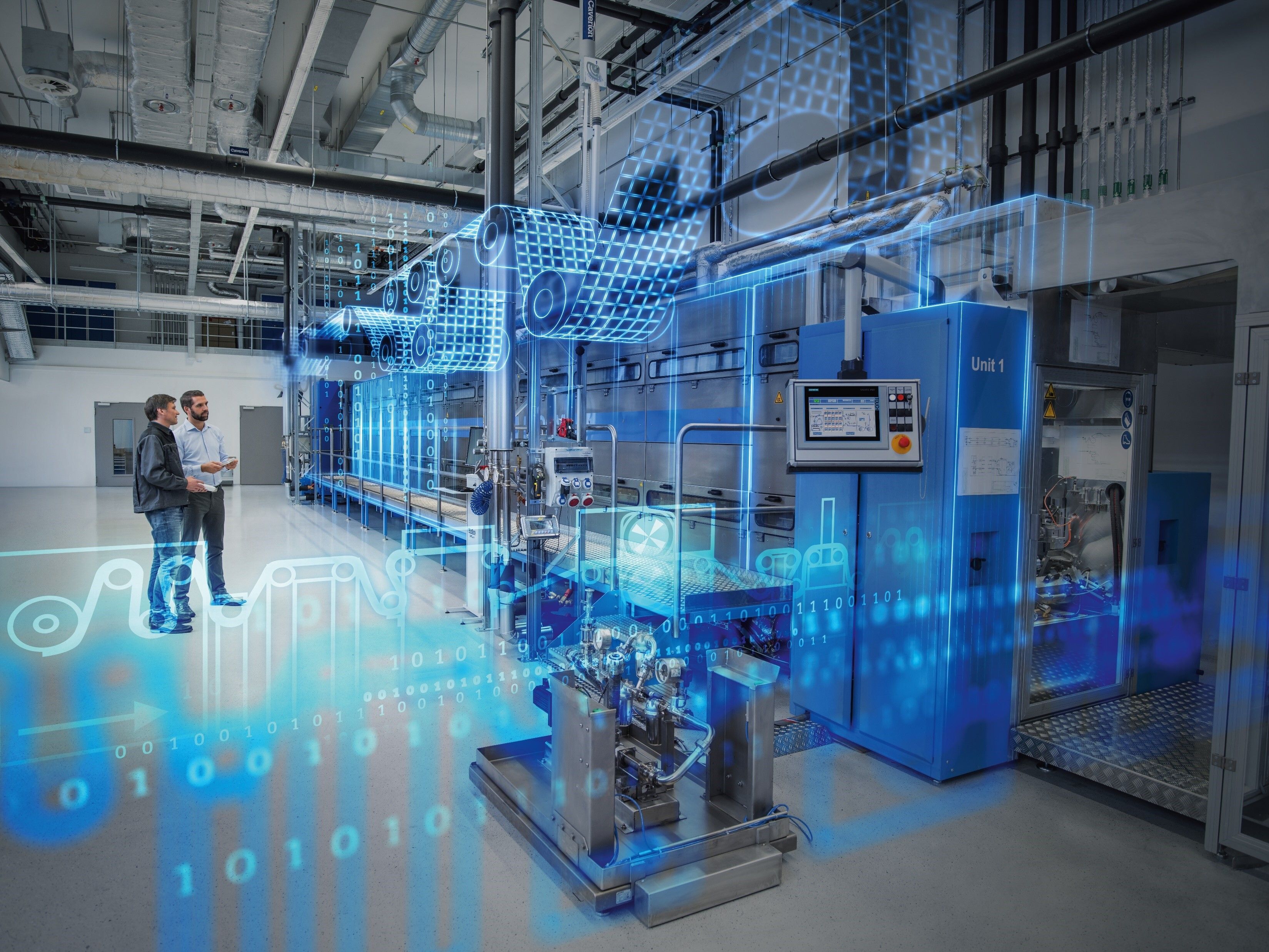
Symbolic image of battery cell production. Image source: Siemens